Steel door rail machines are usually composed of multiple components, including a frame, power system, transmission system, mold and control system. These components work together to process steel into the required rail shape through processes such as cold bending and profiling.
Working principle of Steel Guide Rail Machine
The working principle of the steel door rail machine is relatively complex, but it can be roughly summarized as the following steps:
The raw material (such as steel) is fed into the equipment, and the transmission system is driven by the power system to squeeze and bend the raw material in the mold.
The shape of the mold determines the final shape of the rail, so the design and manufacturing accuracy of the mold are crucial to the quality of the rail.
During the processing, the control system accurately controls the various parameters of the equipment to ensure that the size, shape and accuracy of the rail meet the requirements.
Application field
Steel door rail machines are widely used in construction, transportation, home furnishing and other fields. For example, in the construction field, the steel door guide machine can be used to produce guide rails for various steel doors, such as anti-theft doors, fire doors, etc.; in the transportation field, it can be used to produce guide rail components for transportation tools such as subways and light rails; in the home field, it can be used to produce guide rails for various sliding doors and folding doors.
Equipment Features
High precision: The steel door guide machine adopts advanced control systems and transmission systems to ensure the processing accuracy and shape accuracy of the guide rails.
High efficiency: The equipment adopts automated production methods, which can greatly improve production efficiency and reduce production costs.
Flexibility: The equipment can be customized according to different needs to meet the requirements of different customers for the shape, size and accuracy of the guide rails.
Durability: The equipment adopts high-quality materials and advanced manufacturing processes, with high durability and service life.
Feature of Steel Guide Rail Machine
High production efficiency
The steel door guide machine integrates an advanced automatic control system, which enables fully automated operation from feeding to forming. This automation not only reduces manual intervention and reduces errors caused by human factors, but also greatly improves production efficiency. By accurately controlling the time nodes and process parameters of each link, the equipment can continuously and stably output high-quality products to meet the needs of large-scale production.
High processing accuracy
The equipment uses high-precision rollers and molds. The accuracy of these key components directly affects the processing quality of the guide rails. With the precise control system, it can ensure that the processing accuracy of the track guide rollers meets or even exceeds the design requirements. High-precision processing not only improves the appearance quality of the product, but more importantly, it ensures the performance stability and service life of the product. This is especially important for occasions that require high-precision guide rails, such as high-end buildings, transportation vehicles and other fields.
Stable and reliable
The steel door guide machine has a sturdy structure and uses high-quality materials, which enables the equipment to maintain stable performance during long-term continuous production. At the same time, high-quality materials also improve the durability of the equipment and extend its service life. The stability and reliability of the equipment not only reduces downtime and maintenance costs, but more importantly, it ensures the continuity and stability of the production line, thereby improving overall production efficiency and product quality.
Flow Chart of Steel Guide Rail Machine
Decoiler — Feeding Guide Device — Rolling Forming System — Hydraulic Cutting Device — Run Out Table
Benefit of Steel Guide Rail Machine
- Efficient production: Due to the high degree of automation, it can greatly improve production efficiency, reduce production cycle and reduce production costs.
- Energy saving and environmental protection: Compared with traditional processing methods, the molding machine consumes less energy during the processing, while reducing the generation of waste and exhaust gas, which meets environmental protection requirements.
- Easy operation: The equipment operation is simple and easy to understand, and the skill requirements for operators are relatively low, which reduces labor costs and also reduces errors caused by human factors.
- Easy maintenance: The equipment structure is reasonably designed and easy to maintain.
Component of Steel Guide Rail Machine
Machine Parts
1) Feeding
2) Rollers of guide rail machine
3) Forming cutter
4)PLC Control system (2 type for choosing)
Easy to operate
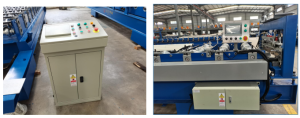
Shutter Door MachineDecoiler (2 type for choosing)
- Manual decoiler 2. Hydraulic decoiler
Applications of rolling up door machine